The Hidden Cost of Solvent Cleaning
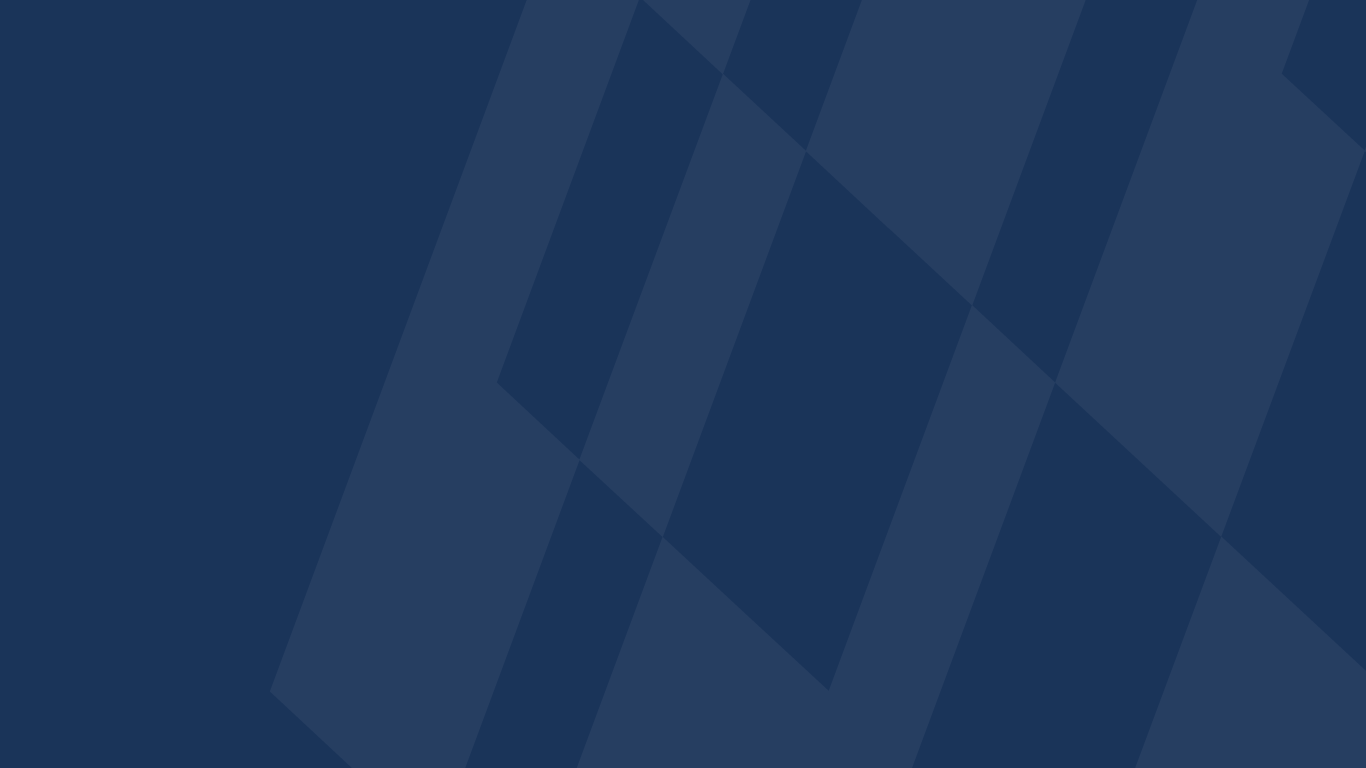
The high cost of traditional practices: why it's time to rethink solvent-based cleaning
The Cost of Traditional Practices
The Coatings Industry Is Under Pressure
The coatings industry is at a crossroads. Narrower margins, tightening environmental regulations, and rising expectations for safety and sustainability have reshaped the competitive landscape.
In this high-stakes environment, industry leaders can no longer afford to ignore the cost of traditional practices.
Through our work with leading coatings manufacturers, we’ve identified recurring challenges that threaten industry profitability and growth.
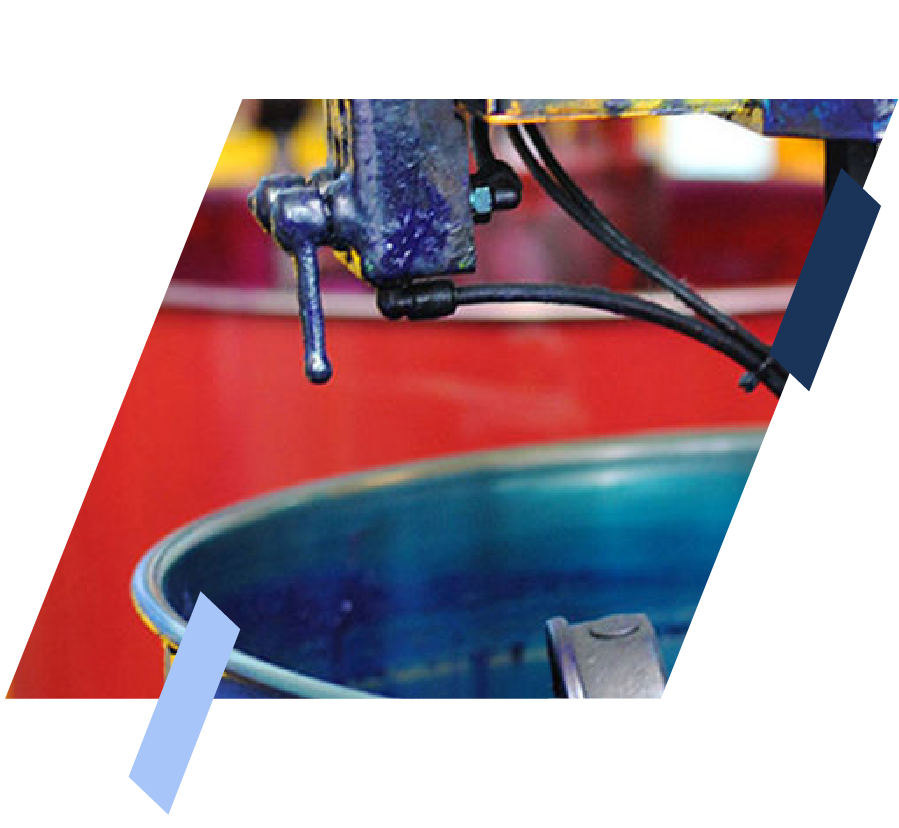
Key Challenges for Coatings Manufacturers
1. Profitability under strain: Rising costs and narrower margins demand optimised productivity to stay competitive.
2. Operational Efficiency: Outdated, time-consuming processes limit throughput, inflate costs, and limit potential production capacity.
3. Site Safety Under Scrutiny: Growing regulatory requirements, heightened safety expectations, and rising employee expectations make proactive risk mitigation essential.
Incremental changes no longer suffice. To meet these pressures, industry leaders must adopt transformative solutions that address these challenges and set a new industry best practice.
The Hidden Cost of Solvents
Here's the reality: There's a hidden cost of using cleaning solvents that silently drains efficiency and profitability, all while creating ongoing, unnecessary risks to both people and the planet.
Eliminating these hidden costs increases net profitability by up to 15%.
The Hidden Costs
Production Inefficiency
Time-consuming and labor-intensive manual cleaning with solvents or caustic creates significant production bottlenecks, drastically reducing efficiency. This slows output by over 250%, limiting production capacity and revenue growth potential.
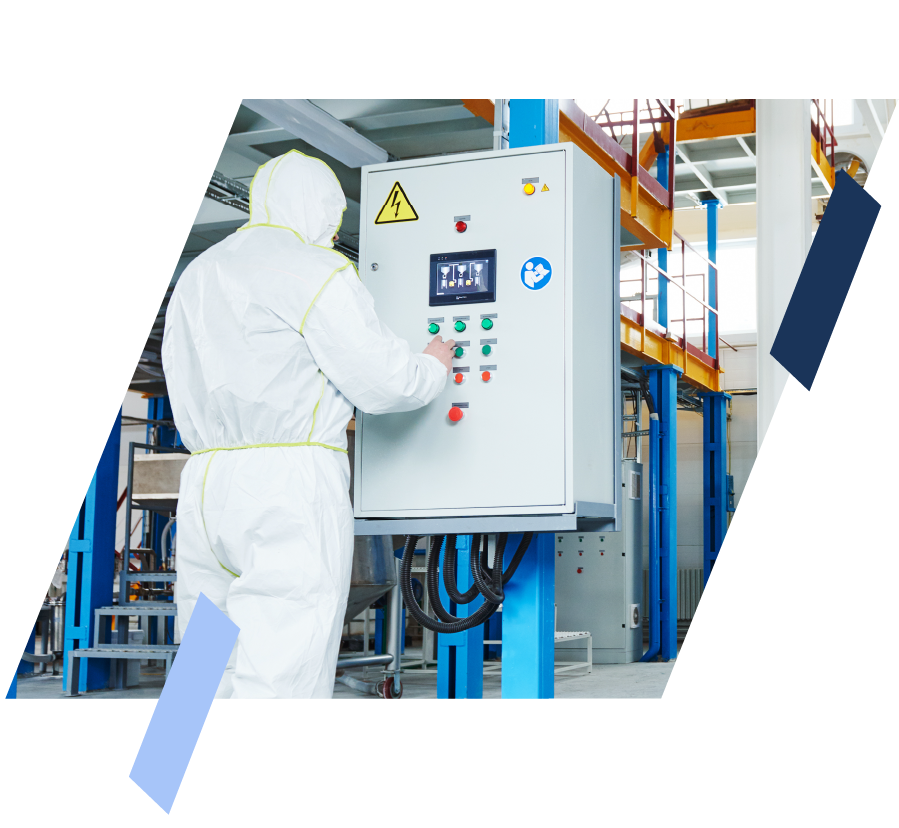
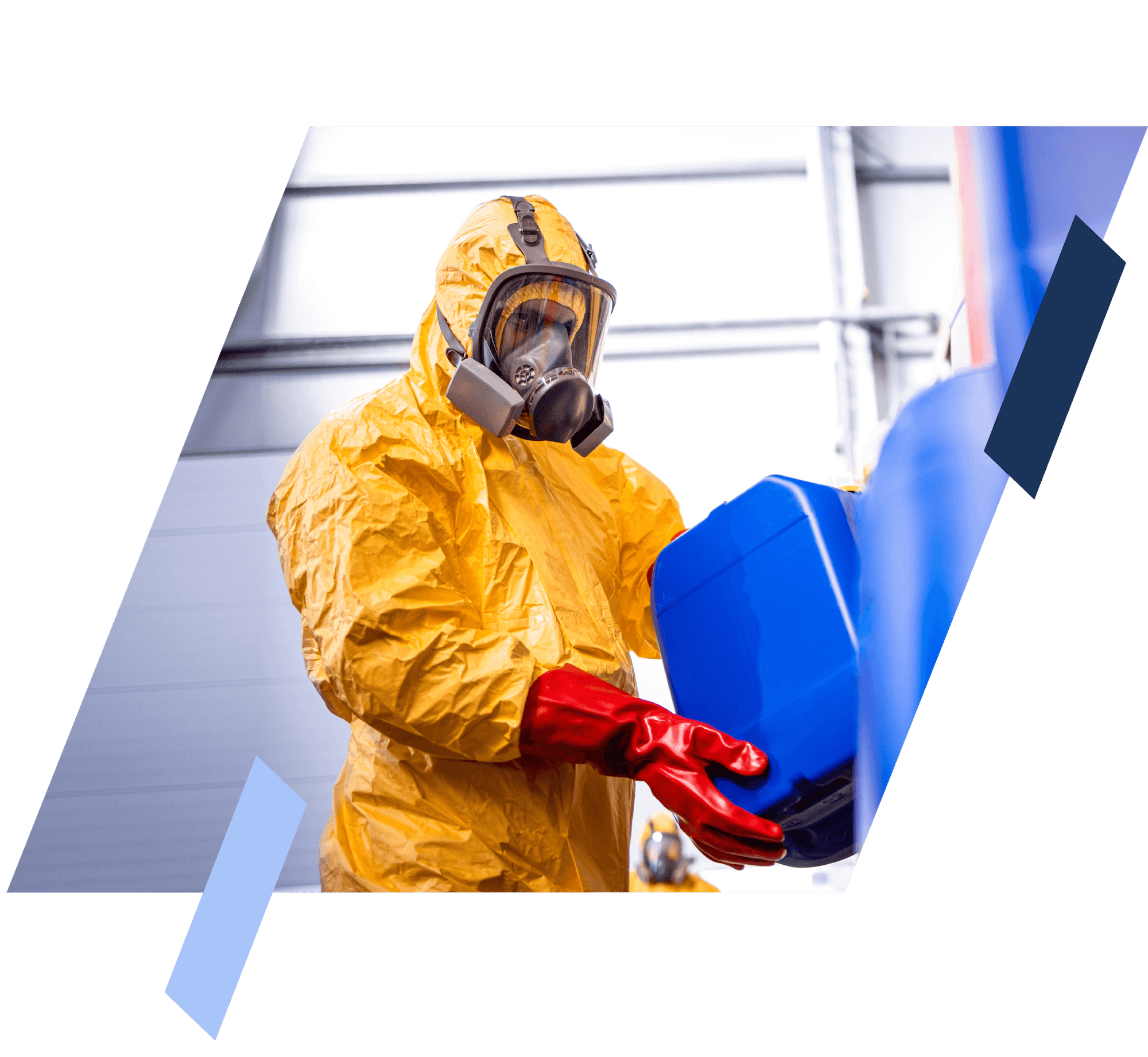
The Hidden Costs
Risk Management
Managing solvents requires complex risk management, including compliance with ATEX zoning regulations and other safety protocols such as PPE.
These measures reduce production flexibility and result in additional costs that erode profit margins.
The Hidden Costs
Product Quality Issues
Poor-quality solvent cleaning leads to lower "right-first-time" production rates and a higher risk of product rejection, driving up rework costs and risking reputational damage that can jeopardize future revenue.
The financial impact can be significant, adding up to 10% of total production costs due to inefficiencies and rework, while rejected products and dissatisfied customers can account for up to 5% of total annual revenue loss.
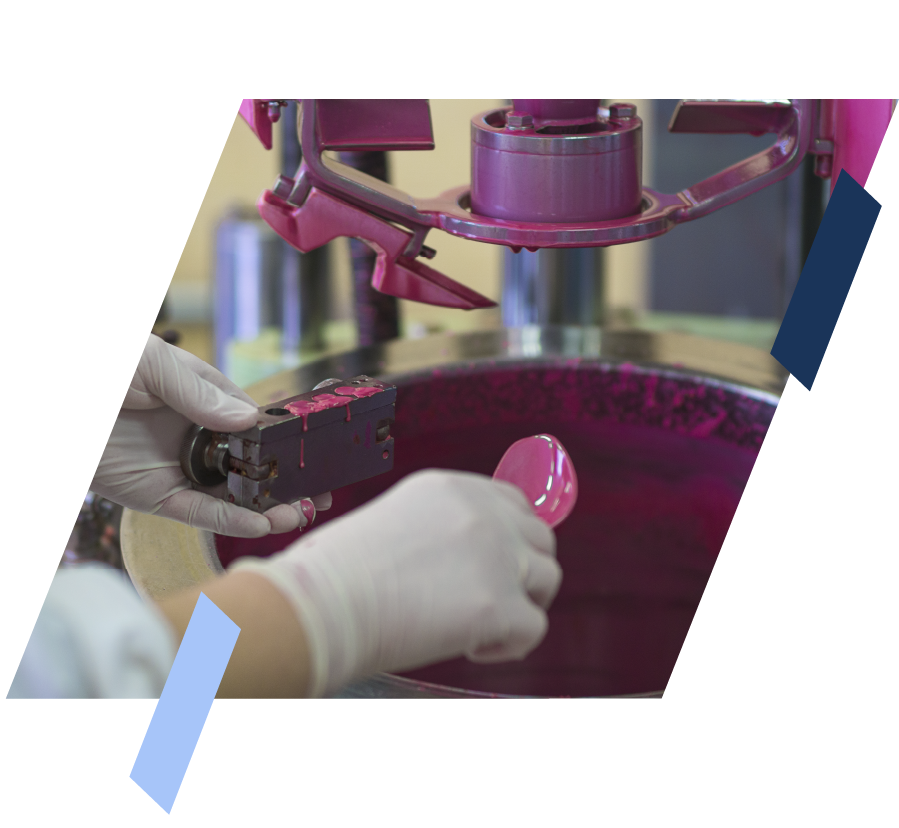
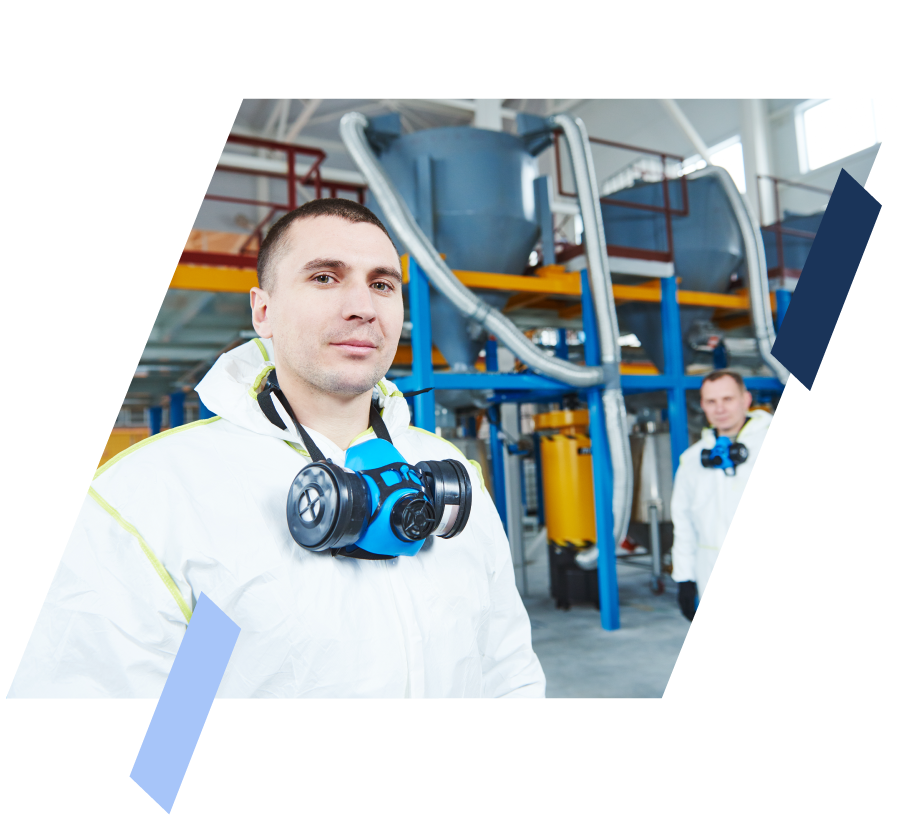
The Hidden Costs
Operator Exposures
Solvent fumes create hazardous and unpleasant working environments. Studies show that 40% of operator exposures stem from cleaning processes, increasing the risk of higher employee turnover and workforce dissatisfaction.
The Hidden Costs
Waste Disposal
Cleaning solvent usage results in high volumes of hazardous waste which must be removed for processing. This adds cost to the operation and increases risk to operators who handle the waste.
Waste management results in higher operating costs, lower margins, and an increased risk of workplace accidents.
%20(4).png?width=900&height=800&name=Image%20template%20(450%20x%20400%20px)%20(4).png)
%20(5).png?width=900&height=800&name=Image%20template%20(450%20x%20400%20px)%20(5).png)
The Hidden Costs
Environmental Risk
Solvents are a primary source of VOC emissions and hazardous waste during production. Controlling these emissions and managing waste disposal significantly increases operating costs and complexity, further squeezing profit margins.
The hidden costs make cleaning solvent usage increasingly untenable. They negatively impact the financial health of the business and are fundamentally incompatible with the requirements of a modern, efficient, and sustainable operation.
Rethink What's Possible
A Future Without Cleaning Solvents?
What if we could reinvent core cleaning operations in coatings to evolve beyond the risks, costs, and inefficiencies of solvent-based cleaning?
A new industry best practice where:
- Production is optimised. Faster, more flexible processes increase throughput without compromising quality.
- Safety is prioritised. Employees are no longer exposed to flammable, carcinogenic solvents, creating safer, healthier workplaces and higher rates of employee satisfaction.
- Profit margins grow. Regulatory risks diminish, high-quality production scales, and streamlined operations drive down costs, securing financial stability.
- Environmental impact is minimised. Hazardous waste and VOC emissions become relics of the past, positioning your business as a sustainability leader.
This isn’t a distant dream. It’s a new best practice – a solvent-free approach that transforms your business for the better, driving cost savings, efficiency, and market competitiveness to ensure resilience and growth in an ever-evolving industry.
The New Industry Best Practice
Ambimization®
Leading manufacturers like Jotun and Sherwin-Williams are already transitioning to this new best practice. Removing harmful and dangerous cleaning solvents from their operations, and replacing them with Ambimization®.
A safer, smarter, and more profitable choice that has redefined equipment cleaning in manufacturing.
Unmatched Advantages
The Benefits of Ambimization®
Ambimization® is a patented, industry-proven methodology that reinvents cleaning through a combination of advanced mechanical engineering and proprietary water-based chemistry.
- Safety First: Water-based fluids are non-toxic, non-flammable, and non-carcinogenic, with low VOC levels. This makes them significantly safer for operators and the environment.
- Efficiency Automated: State-of-the-art machinery and flexible deployment methods reduce manual processes, delivering fast and effective cleaning that improves throughput.
- Quality Without Compromise: Handles even the toughest contaminants – cured epoxies, polyurethanes, and UV-curable resins - improving "right-first-time" rates and reducing the cost of rework.
- Environmental Impact: Self-cleaning properties enable fluid reuse of up to 50 times, resulting in 98.7% VOC reduction, 80.4% waste reduction, and 93.82% carbon savings.
- Cost Savings: Realise up to a 38.7% reduction in operating costs and significant labour savings, positively impacting margins and net profit.
Read our Scott Bader Customer Story to learn more about the benefits of Ambimization®→
Patented Innovation
How Ambimization® Works
Ambimization® is a patented, industry-proven technology that combines advanced mechanical engineering with proprietary water-based chemistry.
Different machines and methods of fluid deployment are used to maximise the penetration of the fluid into the contaminant.
Unlike solvents that dissolve contaminants, Ambimization® fluids lift residues from the substrate by altering surface tension. These residues naturally separate in the fluid, allowing for reuse of up to 50 cycles – dramatically reducing VOC emissions and waste.
Schedule a call to learn more →
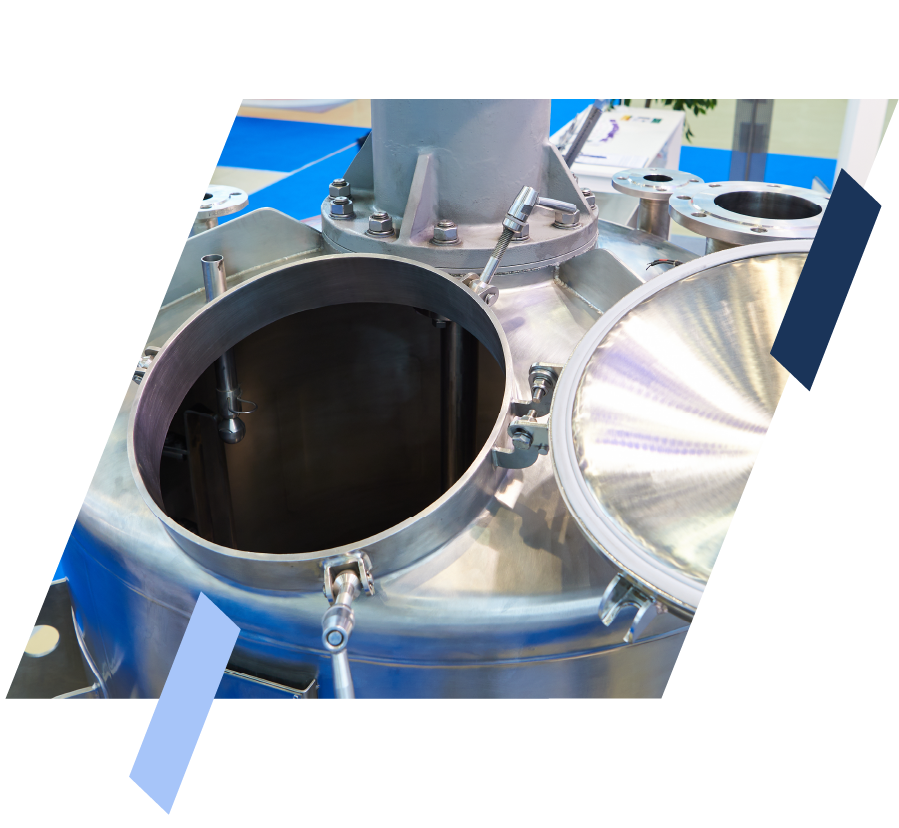
Embracing Transformation
Beyond the Status Quo
As economic, social, and regulatory pressures mount, leaders must act decisively.
Terrafend empowers coatings manufacturers to make a critical transformation with Ambimization® – a clean technology that eliminates the hidden costs of solvents and aligns operations with a model that meets the demands of today – and tomorrow.
Industry leaders have already begun this transformation; now is the time for every coatings manufacturer to act or risk being left behind by competitors who are embracing a safer, more sustainable, and financially resilient future.
Schedule a call to start your transformation →